3 Overlooked Manufacturing Safety Tips for Managers
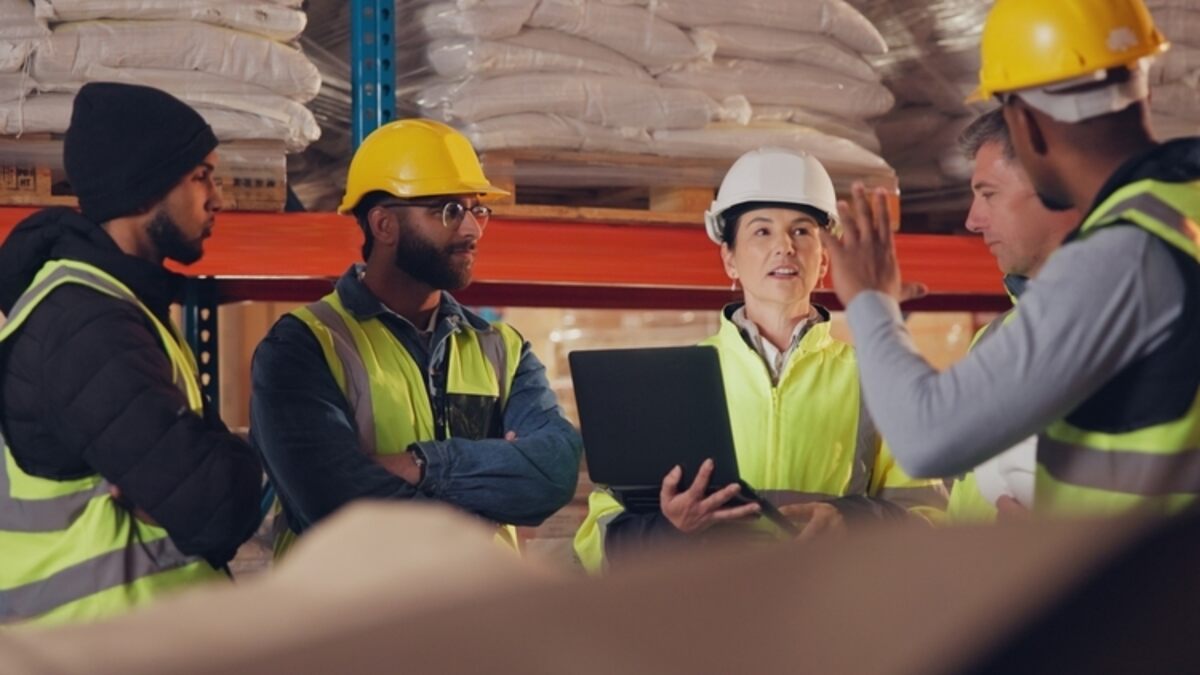
You’ve got slip-and-fall and heavy-lifting protocols covered. But what about less obvious workplace hazards?
Some of the most serious safety risks are easy to overlook or develop so gradually that they escape notice until someone gets hurt. In this article, we’ll explore three less-talked-about safety challenges that manufacturing managers need to address.
More important, we’ll share practical strategies for uncovering hidden risks and a framework for implementing solutions that extend beyond the typical “more training” approach to create truly safer workplaces.
Unseen Safety Hazards in Manufacturing
Airborne Dust
Airborne dust is an issue for most manufacturing facilities, whether it’s from transporting powders, cutting metal, or mixing ingredients. And the health risks can be serious. When workers breathe in dust, the smaller particles can get deep into a person’s lungs, causing respiratory problems like occupational asthma or chronic obstructive pulmonary disease (COPD). Long-term exposure can even lead to chronic conditions like silicosis.
The tricky part? A lot of dangerous dust isn’t easily visible. Here’s how safety managers can spot it:
- Look for dust accumulation on horizontal surfaces
- Use the flashlight beam test (shine it horizontally to see particles in the air)
- Use monitoring tools like air samplers and particle counters
- Screen your employees for eye and skin irritation
Once you’ve identified problem areas, you can tackle them with:
- Good ventilation systems that capture dust at the source
- 100% sealed connectors to contain dust in processing systems
- Regular cleaning with high-efficiency particulate air (HEPA) vacuums
- Wet methods to keep dust down
- Personal protective equipment (PPE), including respirators when needed
- Employee training on dust hazards
Don’t forget to check OSHA’s exposure limits for specific types of dust in your industry. The regulations are there for a reason; dust can seriously impact worker health over time.
Static Buildup
Static buildup is the accumulation of electrical charge on a surface. In manufacturing, this happens when two materials come in contact and then separate, such as during conveying or processing. Some materials (like plastics, synthetic textiles, and certain food powders) are especially prone to generating static electricity.
The biggest danger is when static leads to a spark in environments with flammable vapors, gases, or combustible dust. This can trigger devastating fires or explosions. Employees may also get a nasty electric shock when coming in contact with charged equipment.
Since static electricity is invisible until it discharges, safety managers need proactive ways to identify it, such as:
- Using field meters or static detectors to measure charge buildup on surfaces
- Identifying operations involving friction, separation, or flowing of materials, especially at high speeds
- Asking workers if they’ve experienced shocks or noticed materials behaving unusually
- Looking for unexplained quality problems like materials sticking together improperly
- Tracking malfunctions in electronic components, which can be caused by static buildup
The best approach to managing static is prevention through proper grounding, humidity control, and using static-dissipative materials in high-risk areas. Regular testing and maintenance of these systems is essential, particularly in operations handling flammable materials or fine powders.
Routines
Routine-related injuries occur when workers perform tasks that they’ve done so many times they go into “autopilot” mode.
Workers stop actively looking for risks in familiar tasks. Over time, they may skip safety steps they deem unnecessary based on past experiences where nothing went wrong. A simple replacement of a hose-and-clamp connector could lead to a pinch injury, cuts, or worse.
Since these tasks often escape safety scrutiny precisely because they’re “routine,” safety managers should:
- Regularly review even the most mundane tasks for potential hazards
- Have someone unfamiliar with the task observe and identify risks
- Monitor for increased errors during extended shifts or repetitive work cycles
- Design routine tasks to be as safe as possible even on “autopilot”
Prevention requires a combination of engineering controls, refresher training, rotation of duties, and building a culture where workers understand that familiarity with a task doesn’t eliminate its inherent risks.
How to Escalate Safety Issues
When it comes to workplace safety, not all solutions are created equal. The Countermeasure Ladder helps us think more critically about how we address hazards instead of defaulting to the easiest (but often least effective) solutions.
Too often, we stop at “Let’s train employees better” or “Let’s audit more frequently” when we could be implementing more robust solutions.
Enhance Safety with BFM® fittings
One solution that addresses multiple safety concerns is the implementation of BFM® fittings. These flexible connectors help address many of the unseen safety issues in processing facilities.
- Dust Containment: BFM® fittings create a 100% seal, preventing dust from escaping into the workplace and reducing respiratory hazards.
- Static Dissipation: Static-dissipating materials and equipment reduce the risk of ignition in environments with combustible dust.
- Injury Reduction: The snap-in design requires no tools for installation or removal, dramatically reducing the risk of pinch injuries, cuts, or even the loss of hands or limbs.
By upgrading critical connection points with BFM® fittings, powder processing facilities can address multiple safety concerns and improve operational efficiency.