Three Ways To Improve Efficiency in Powder Manufacturing
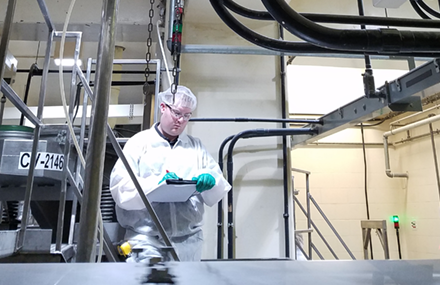
Efficiency in powder manufacturing isn’t just about speed — it’s about strategic optimization that minimizes downtime, reduces contamination risks, and maximizes production potential. For engineering, maintenance, and project managers, the right solutions can transform operational performance and improve bottom-line results. But how do you achieve this? Powder Solutions Inc., the largest U.S. distributor of BFM® fittings, has innovative solutions that can help.
What Does Efficiency in Powder Manufacturing Look Like?
Efficiency is a delicate balance of minimizing waste, reducing equipment downtime, and maintaining consistent product quality. The most successful manufacturers understand that every minute and every connection in their production line counts. Here are actionable ways to improve manufacturing efficiency in your powder handling systems:
1. Minimize Changeovers and Cleaning
Frequent changeovers and lengthy cleaning sessions can cripple production efficiency. BFM® fittings make these processes faster and easier by offering game-changing solutions:
- Material Longevity: Replace fittings less frequently
- Snap-in Design: Enables quick, tool-free installations and replacements
- CIP Compatible: Clean in place to support rapid product transitions
If it sounds simple, it’s because it is. You can streamline operations and save time by choosing solutions designed for quick maintenance.
2. Tackle Common Challenges With Purpose-Built Solutions
Targeted tools and products are critical for solving specific powder handling challenges like contamination, leakage, and testing. BFM® fittings are designed with operational efficiency in mind:
- 100% Sealed Connections: Reduce product loss and harmful dust accumulation
- Standardized Inventory: Simplifies training and reduces potential human error
- Specialty Fittings: Designed for diverse applications, processing, inspection, sealing, and more
Integrating these purpose-built solutions reduces complexity and increases production line uptime.
3. Maximize Equipment Uptime Through Proactive Maintenance
Unplanned downtime can derail production goals. That’s why it’s critical to focus on preventive maintenance, predictive analytics, and reliable products to keep your equipment running smoothly:
- Increased Visibility: Clear connectors allow you to easily monitor processing
- Improved Material Flow: Prevents bridging, accumulation, and other processing issues that impact equipment performance
- Quick Access Port: Drop test balls or take product samples without interrupting production
Reliable, low-maintenance solutions keep your manufacturing lines operational and efficient.
Ready To Optimize Your Powder Manufacturing Process?
Improving efficiency in powder manufacturing doesn’t have to be complicated. Strategies like reducing changeovers, leveraging purpose-built products, and maximizing uptime can make a significant difference. At Powder Solutions Inc., we understand the challenges facing engineering, maintenance, and project managers. Our line of BFM® fittings is designed to support your efficiency goals by eliminating common pain points such as contamination, leakage, and downtime. Explore our inventory today and see how BFM® fittings can transform your production line.