Essential Powder Handling Equipment for 0 Safety Incidents This Year
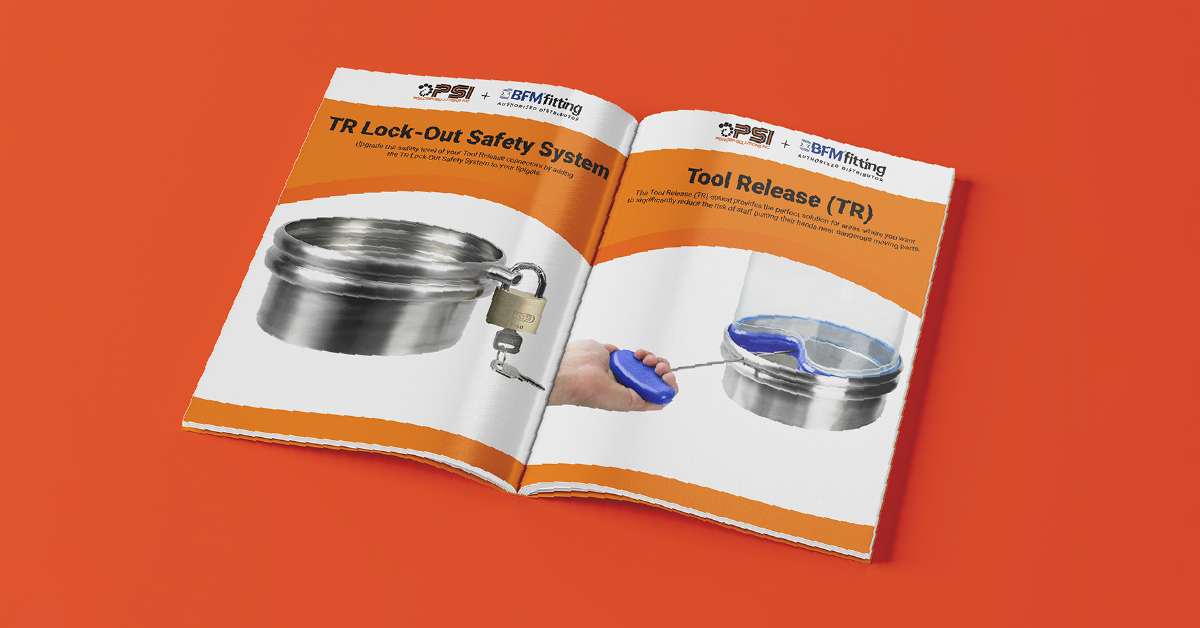
The good news? With the right powder handling equipment and safety protocols, these incidents are avoidable. This guide explores how BFM® fitting solutions can dramatically reduce risk factors and help you achieve zero safety incidents this year.
Understanding Powder Processing Hazards
Before we discuss solutions, let’s examine the primary hazards in powder processing environments:
Dust Explosions
When combustible dust becomes airborne and encounters an ignition source, the result can be devastating. Primary explosions can trigger even more dangerous secondary explosions as accumulated dust is disturbed.
Static Electricity
The movement of powder naturally generates static electricity. Without proper dissipation, static can build to levels sufficient to spark combustible dust or flammable vapors.
Operator Hazards
Working in a processing facility is full of risks for workers. Besides the dangers of breathing in dust, pinch-point injuries are common, especially from replacing hose-and-clamp connectors. Changeouts and cleaning also put workers in potentially dangerous proximity to moving equipment.
Contamination Risks
Poorly sealed systems not only create dust hazards but can also allow cross-contamination—a critical concern in food, pharmaceutical, and chemical processing.
Basic Safety Features of BFM® fittings
BFM® fittings were originally created to contain dust that hose-and-clamp connectors could not contain. Over the past several years, however, BFM® engineers have expanded their products to solve many more safety issues that come with powder processing. But before we get into specialized safety solutions, let’s talk about the basic safety features of BFM® fittings.
Explosion Resistance
BFM® fittings are explosion resistant in two ways. First, they are 100% sealed and therefore contain the dust that could otherwise leak into the facility. This dramatically reduces both primary and secondary dust explosion risks. Second, if an explosion does occur, BFM® flexible connectors can contain a blast exceeding 60kPa.
Static Dissipation
BFM® flexible connectors are made from a static dissipative material. Rather than insulating or conducting a charge, they can help dissipate electricity safely. Combined with proper grounding procedures, this significantly reduces the risk of a static spark.
Tool-Free Installation
BFM® fittings do not require tools for installation or removal, eliminating potential injuries from sharp tools or fasteners.
Regulatory Compliance
For all these reasons and more, BFM® fittings conform to leading international safety standards, helping facilities maintain compliance with regulatory requirements.
Essential Safety Equipment Solutions
Beyond these foundational safety features, BFM® offers specialized powder-handling equipment to address specific safety concerns.
Enhanced Access Control Options
Tool Release (TR): This system requires a rod tool for connector removal, significantly reducing the risk of operators placing hands near dangerous moving parts. For facilities requiring enhanced security, the Smiley variant adds an extra level of equipment safety by requiring a unique Smiley Face Tool for connector removal. This controlled access ensures that only authorized personnel can disassemble connections.
TR Lock-Out Safety System: Building on the TR foundation, this system adds another security layer by controlling access via a standard padlock. This makes it compatible with existing lockout/tagout programs and provides visual confirmation that the system is secured.
Specialized Connectors for High-Risk Environments
Seeflex 060ES: For applications involving pressure risks, this reinforced sleeve restricts stretching. Capable of handling over-pressure applications up to 24.7 PSI, it provides containment security while maintaining the easy-change benefits of the BFM® system.
Kevlar Cover: This flame-retardant cover fits over existing connectors and is specifically designed for potentially explosive applications. The material’s inherent fire resistance reduces ignition risks while maintaining the flexibility needed for powder processing connections.
Monitoring and Maintenance Safety
Pneumatic Monitor System: This simple-to-install pressure monitor system alerts operators when connectors are removed and installed. Real-time monitoring prevents accidental startups during maintenance and provides verification that connections are properly reinstalled before operations resume.
Building a Safety Strategy
Achieving zero incidents requires more than just purchasing equipment—it demands a strategic approach:
1. Risk Assessment
Examine your specific process hazards. Which areas handle combustible dust? Where do maintenance operations create the greatest exposure to moving parts? Where are pressure conditions most variable? Document these risk zones to prioritize safety implementations.
2. Prioritize Investments
While a facility-wide upgrade to BFM® systems provides the greatest safety benefit, most operations need to phase in improvements. Start with high-risk areas: connections handling combustible materials, areas with frequent maintenance requirements, or zones with historical incident patterns.
3. Develop Comprehensive Protocols
Equipment alone cannot ensure safety. Develop clear procedures for installation, inspection, and maintenance of BFM® fittings. Train operators thoroughly on both the mechanical aspects and the safety rationale behind proper use. Implement regular inspections of all connection points.
Get to 0 Incidents With the #1 BFM® fitting Distributor
The path to zero safety incidents in powder processing facilities isn’t found through addressing incidents after they occur—it’s built by systematically eliminating risk factors before they can lead to dangerous situations.
BFM® fittings provide both the foundational safety improvements and specialized solutions needed to create safer powder processing environments. Contact PSI today to discuss which BFM® solutions best fit your facility and take the first step toward a zero-incident year.