Ensuring Absolute Containment in Pharmaceutical Powder Processing: The Role of the BFM® Fitting
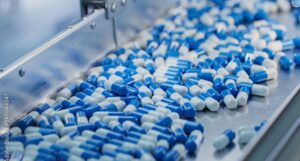
In the pharmaceutical industry, where product purity and safety are paramount, maintaining absolute containment of high-potency powders is critical. Even small breaches in containment can lead to significant health risks for workers, contamination of the environment, and compromised quality of the final product. Pharmaceutical powder processors must ensure that powder does not escape during processing, transport, or handling, as any leakage could create hazardous conditions both inside the plant and in the wider community.
The Risks of Powder Leakage
When pharmaceutical powders leak from processing equipment, they can form dust clouds that pose multiple dangers. Inhalation of airborne powder particles can lead to serious respiratory issues for plant workers, especially when dealing with highly potent active pharmaceutical ingredients (APIs). Additionally, the risk of cross-contamination between different batches of product becomes a major concern. For example, even a tiny amount of a different product contaminating a batch could result in costly recalls, regulatory scrutiny, or damage to a company’s reputation.
Despite the high stakes, many pharmaceutical plants continue to rely on outdated methods for connecting processing equipment—such as flexible connectors and hose clamps. These older connections are often prone to leakage and powder buildup, requiring operators to spend significant time and effort ensuring a tight seal. Unfortunately, these connections still leave room for potential contamination, leakage, and inefficiency in the system.
Introducing the BFM® Fitting: A Revolutionary Solution
Enter the BFM® fitting—an innovative solution to the problems that plague traditional hose clamps and flexible sleeves. The BFM® fitting is engineered to provide pharmaceutical powder processors with a reliable, leak-proof connection between process equipment, ensuring the highest level of containment and product integrity.
How the BFM® fitting Works
The BFM® fitting consists of two main components: a flexible sleeve and two stainless steel snap bands. The flexible sleeve is made from high-quality, airtight material that is designed to fit securely over specially formed spigots, which are welded into place on the processing equipment. These components are easily assembled by hand, with no tools required for installation. The BFM® fitting’s snap-fit design ensures a tight, secure seal that prevents powder from escaping at the connection points.
This innovative fitting design is not only airtight but also completely free of crevices or folds. This smooth, continuous surface eliminates the common issue of powder buildup that can occur with traditional connections. Without areas where powder can collect, cleaning and sanitization processes become significantly more efficient, improving both safety and compliance with stringent pharmaceutical industry standards.
The Benefits of the BFM® Fitting for Pharmaceutical Processing
- Complete Containment: The BFM® fitting ensures a complete seal, preventing any powder leakage during the processing or transfer of high-potency pharmaceutical ingredients. This eliminates the risks of airborne dust clouds that could harm workers and cause cross-contamination.
- Enhanced Safety for Workers: By preventing the escape of fine powder particles, the BFM® fitting reduces the likelihood of respiratory hazards. Workers can operate in a safer environment with less risk of exposure to harmful substances, improving overall workplace health and safety.
- Improved Product Integrity: With no leakage, you can be confident that your batch of pharmaceutical product remains intact and free from contamination. The BFM® fitting helps to ensure that the product being processed is pure, consistent, and compliant with industry regulations.
- Easy Installation & Maintenance: The design of the BFM® fitting makes installation and removal quick and simple, requiring no special tools. The snap-fit design also allows for easy inspection and maintenance, reducing downtime and keeping the production line running smoothly.
- Superior Sanitation: The crevice-free design of the BFM® fitting ensures that powder does not accumulate in hard-to-reach areas, simplifying cleaning procedures. In an industry where sanitation is critical, the BFM® fitting helps maintain compliance with good manufacturing practices (GMP) by reducing contamination risks.
- Customizable for a Wide Range of Applications: Whether you’re processing API powders, filling lines, or working with baghouses, the BFM® fitting can be customized to fit various process equipment in your pharmaceutical plant. This versatile solution is ideal for applications such as:
- Filling lines
- Sifters and sieves
- Baghouses and cyclone discharges
- Load-out chutes
- Conveyors
- And many more
Conclusion: A Smart Investment for Pharmaceutical Manufacturers
The BFM® fitting is more than just a connector—it’s a key part of an integrated solution for maintaining the highest standards of product quality, worker safety, and operational efficiency in pharmaceutical powder processing. By replacing outdated flexible connectors and hose clamps, the BFM® fitting helps pharmaceutical manufacturers mitigate the risks of powder leakage and contamination while improving productivity and reducing operational costs.
In an industry where precision and safety are paramount, the BFM® fitting is a smart, long-term investment for any pharmaceutical processing plant aiming to stay ahead of evolving safety standards and ensure the delivery of safe, high-quality products to consumers.